International tyre recyclers eye UK market as sun sets on waste exports
New technologies address the continuing growth in end of life tyre waste
The UK has often been all too ready to deal with its end of life tyres (ELTs) by exporting the problem to developing nations. The country’s – and many other developed western nations’ – willingness to export waste as a cheaper alternative to dealing with waste product domestically has led to government action both at home and abroad. India, a key market for UK waste exporters, joined several South East Asian countries in introducing measures to counter the growing problem of foreign waste stockpiling and pollution this year. Meanwhile the UK government’s Environment Bill, refreshed since the 2019 general election in the early months of 2020, promises “powers which will allow government to stop the export of waste…to developing countries.”
The Tyre Recovery Association secretary general, Peter Taylor called for action from the tyre market in February when he said: “The true cost of tyre recycling has long been masked by artificially low pricing for exported waste especially to India.” Into this context we have seen a number of new announcements relating to tyre recycling in the UK over the last month, including new players and technologies entering the market.
Below, Tyrepress reports the latest news from the sector.
EA allows portside tyre shred storage, updates advice
TRA welcomes new portside storage rules

The UK Environment Agency has allowed portside tyre shred storage, but there are numerous provision and a time-limit associated with the latest advice (Photo: Peter H; Pixabay)
On 3 July 2020 the UK government issued advice on the port-side storage of tyre shred via a time-limited Environment Agency Regulatory Position Statement (RPS 238). RPS 238 was updated on 15 September 2020 and lasts until 30 June 2021. In short RPS 238 clarifies when you can store PAS 107 certified clean cut tyre shred and chip at a port before you export it. This advice only applies to those that apply for a permit to store PAS 107 certified clean cut tyre shred and chip by 29 January 2021.
BASF invests 16 million euros into Pyrum waste tyre oil recovery
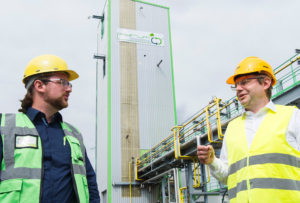
Pascal Klein (left), founder and CEO of Pyrum Innovations AG and Dr. Christian Lach (right), Project Lead ChemCyclingTM at BASF, in front of Pyrum’s tyre pyrolysis plant in Dillingen/Saar Germany. (Photo: BASF)
BASF SE has announced that it is investing 16 million euros into Pyrum Innovations AG, a technology company specialized in the pyrolysis of waste tyres, headquartered in Dillingen/Saar, Germany. With the investment, BASF will support the expansion of Pyrum’s pyrolysis plant in Dillingen and the further roll out of the technology. BASF’s Pyrum investment follows the company’s partnership with New Energy, a similar tyre-derived oil project based in Budapest, Hungary at the start of September 2020.
BASF partners with New Energy in tyre-derived oil project
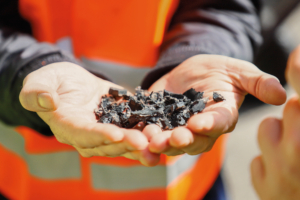
Shredded tyres before being processed into pyrolysis oil by New Energy, a technology company which supplies BASF with up to 4,000 metric tonnes of tyre-derived pyrolysis oil per year (Photo: BASF)
BASF SE has signed an uptake supply agreement with New Energy, which specializes waste tyre pyrolysis and is headquartered in Budapest, Hungary. According to the agreement, New Energy will supply BASF with up to 4,000 metric tonnes of pyrolysis oil per year derived from waste tyres. In a pilot phase, the first volumes of the pyrolysis oil have already been used in BASF’s integrated chemical production site in Ludwigshafen, Germany.
Tyre recycling and energy generation – why the time is now
IRR Waste 2 Energy discuss the reasons for increased innovation and interest in end of life tyre recovery in 2020
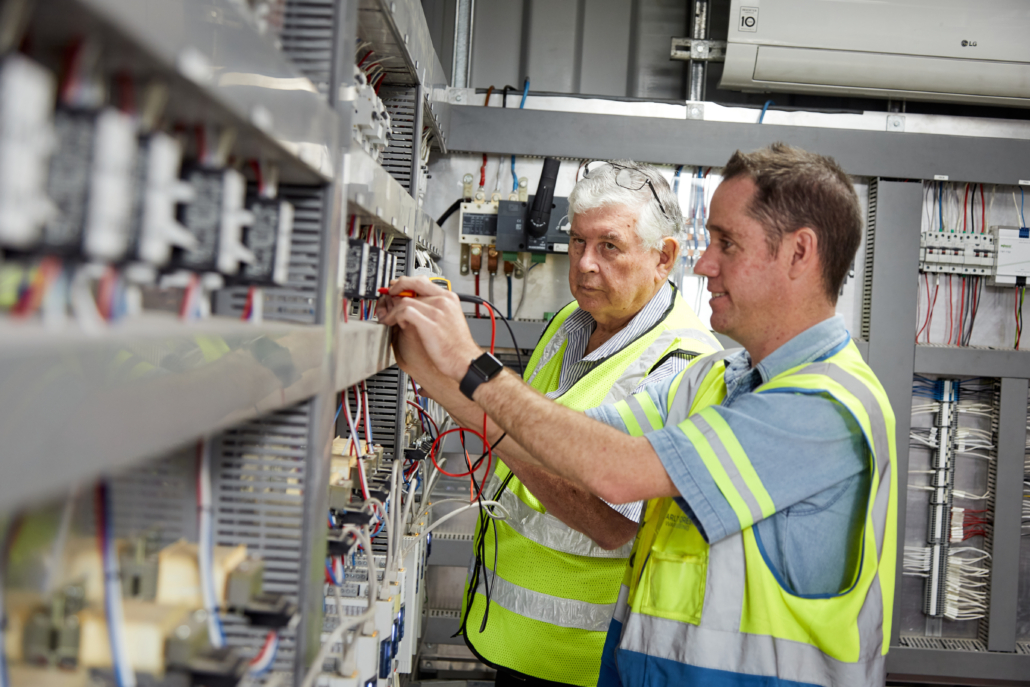
IRR Waste 2 Energy’s continuous pyrolysis plant (Photo: Shaun Flannery/shaunflanneryphotography.com)
Early in 2020 the UK government suggested a tentative plan to ban the export of all end of life tyres (ELTs). The timing was unfortunate, with the challenges of the rest of 2020 becoming increasingly apparent at the start of spring. However, with strict recycling, energy from waste, and environmental targets to meet over the next twenty years or so, many companies are pressing ahead in raising awareness and innovating within the broad recycling sector. ELTs represent a particularly important part of the new era in recycling introduced by the UK’s Environment Bill, not least because of new and incoming measures internal and external against used and end of life tyre exports, a popular, yet often damaging solution to the problem. Rory Hughes, technical director at IRR Waste 2 Energy, and a waste and recycling expert with more than 35 experience in the industry, told Tyrepress why adopting a more holistic approach to tyre recycling is the way forward.
Carlton Forest offers ‘visionary’ new tyre recycling technology
A new pyrolysis-based tyre recycling technology is to help achieve targets set out by the Government Environmental Plan, according to the Carlton Forest Group. Subsidiary Carlton Forest IRR Waste 2 Energy will exclusively supply its continuous pyrolysis technology to businesses, urban regeneration schemes and local authorities across the UK. Established in South Africa in 2006, IRR was acquired by the Carlton Forest Group in 2018. “Our technology is quite simply game changing and presents new opportunities for the UK to explore how it can responsibly deal with its hard to recycle waste, such as end of life tyres,” said Graham White, group commercial director at Carlton Forest Group.
Could continuous pyrolysis deliver savings for tyre manufacturers?
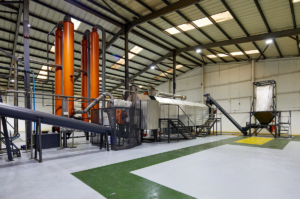
IRR Waste 2 Energy’s continuous pyrolysis plant – the first in the UK – at parent company Carlton Forest Group’s Worksop HQ (Photo: Shaun Flannery/shaunflanneryphotography.com)
Waste rubber generated by tyre manufacturing could deliver increased energy savings and business opportunities according to IRR Waste 2 Energy. The company’s continuous pyrolysis technology, which is fully commissioned and in operation at its parent company Carlton Forest Group’s Worksop headquarters, has delivered “tangible results” in both “energy generation and the production of by-products such as pyrolysis oil and carbon char,” the company states. These materials can be refined further to produce high grade engine oil and recovered carbon black (RcB).
Carlton Forest Group appoints Scott Robson financial director
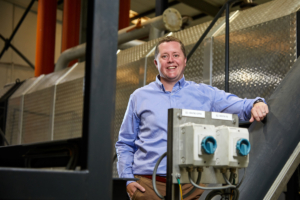
Scott Robson, financial director at Carlton Forest Group (Photo: Shaun Flannery/shaunflanneryphotography.com)
Carlton Forest Group has appointed a new financial director as it enters the next phase of its growth strategy. Scott Robson has joined the waste to energy company, home to the UK’s only continuous tyre pyrolysis plant. Originally from Leeds, Robson has a global career in director level finance roles. “We extend a very warm welcome to Scott and look forward to working with him as our portfolio of business continue their exciting growth phrases and strategic diversification,” said Mark Pepper, CEO, Carlton Forest Group Holdings. “He joins our driven and dynamic senior team and we know that he will have a long and successful career with us.”
Michelin coordinates 16 million euro BlackCycle tyre circular economy project
Michelin is coordinating 7 industrial partners, 5 Research & Technological Organizations (RTOs) and an innovation cluster into a European consortium designing pioneering processes to produce new tyres from end-of-life tyres (ELTs). The project, called BlackCycle owing to its focus on developing a circular economy for tyres, is run across five countries. Officially funded by the EU in May 2020 (specifically by the European Union’s Horizon 2020 research and innovation programme under grant agreement No 869625), the BlackCycle par announced the launch of the project on 3 September 2020. The BlackCycle project involves 13 organisations in a European public-private partnership aims to demonstrate the technical, environmental, and economic viability of circular processes.
Enviro: Improved tyre pyrolysis market will help revenues
Scandinavian Enviro Systems AB is reporting a “dramatic increase in interest” the pyrolysis oil the company extracts from end-of-life tyres. According to the company, the oil has a high bio content due to the natural rubber in tyres and is therefore “of great interest to many players in the market because it could replace fossil-based alternatives”. This, in turn, is likely to help Enviro’s sales revenues. “Based on the market response and our own calculations, we judge that the oil recovered from end-of-life tyres could contribute to a strong increase of revenues from recycling plants that use our technology,” Thomas Sörensson, CEO of Enviro, explained.
Peel completes Engineering Definition phase for Powerhouse DMG plant site
Powerhouse Energy Group’s first hydrogen production from waste plastic (including end of life tyres) plant has received a boost, as the first phase of engineering work on its site at Cheshire’s Protos Energy Park was completed on time, despite the Coronavirus lockdown. Peel L&P completed the Engineering Definition stage of the contractors’ work for the DMG plant on schedule. The completion of detailed site definition drawings and procument packages for equipment and components will enable delivery contractors to price their contracts for constructing the plant and the associated on-site buildings.
Allan Vlah, Tim Yeo join Powerhouse Board as non-executive directors
UK technology company Powerhouse Energy Group has appointed Allan Vlah as a non-executive director with immediate effect. With twenty years’ experience in the investment industry, Vlah (43) is a director in Aviva Investors’ infrastructure group where he started and continues to lead Aviva Investors’ Energy from Waste equity strategy. Powerhouse commercialises hydrogen production from waste plastics, including end of life tyres. Further to the completion of its acquisition of Waste2Tricity Limited, Powerhouse also appointed Tim Yeo as a non-executive director with immediate effect. Yeo has wide experience in government, serving in the Environment and Health Departments, and subsequently as Shadow Secretary of State for Trade and Industry in the Shadow Cabinet. He is currently the chairman of the New Nuclear Watch Institute, Honorary Ambassador of Foreign Investment Promotion for South Korea and since 2007 has been a non-executive director of Getlink SE, operator of the Channel Tunnel whose market capitalisation on the Paris Bourse exceeds £6 billion.
Planning permission granted for Powerhouse DMG process facility in Cheshire
Powerhouse Energy Group has developed a proprietary process technology known as DMG. This can convert waste plastic, end-of-life-tyres, and other waste streams efficiently and economically into syngas. Valuable products such as chemical precursors, hydrogen, electricity and other industrial products may be derived from this syngas. The technology is one of the world’s first proven, modular, hydrogen from waste (HfW) process.
The Powerhouse DMG process can generate up to two tonnes of road-fuel quality H2, and more than 58MWh of exportable electricity per day. It produces low levels of safe residues and requires a small operating footprint, making it suitable for deployment at enterprise and community level.
Sunderland chosen as site for ‘UK’s greenest’ tyre recycling plant
Norwegian recycling company Wastefront and Sunderland City Council have signed a deal to build the new facility in Port of Sunderland
Norwegian waste tyre recycling company Wastefront has chosen Port of Sunderland as the location for its first plant. Construction will begin in 2021. The company says that on completion it will be “the greenest waste tyre recycling plant in the UK.” The plant will convert locally-sourced End-of-Life Tyre (ELT) waste into useful commodities, including liquid hydrocarbons and carbon black, which can then be reutilised in processes such as alternative fuel or ground rubber manufacturing. The construction of the plant is expected to generate around 100 jobs in the region and, once fully up and running in the second half of 2022, the plant will employ up to 30 people full time. It is estimated the investment will be around £25 million.
Norwegian startup choses UK for first tyre recycling plant
Norwegian tyre recycling startup, Wastefront AS has confirmed that its first plant will be located in the UK. It plans to invest between £20-30 million on the recycling facility, with its construction resulting in employment for around 100. When fully up and running, Wastefront adds the plant will employ between 20 and 30 people full time. The company, founded in 2019 in Oslo, is now deciding where to locate its first site. The company tells Tyres & Accessories that its plant will be the first to combine conventional technology with Wastefront’s own proprietary technology, which will minimise the environmental impact typically associated with traditional tyre pyrolysis. It adds that this will “make the UK plant the ‘greenest’ of its kind.”
Wastefront uses pyrolytic reactors to break down tyres using thermal decomposition – a process commonly known as pyrolysis. Wastefront’s pyrolytic reactors comply with all local environmental regulations, it says. And the company also works to ensure compliance with all planned future regulation updates.
Wastefront appoints ex-Wintershall DEA deputy CEO, COO as chairperson
Norwegian tyre recycling startup Wastefront, has appointed Maria Moræus Hanssen as its chairperson. Heading up Wastefront’s board, Hanssen brings international experience from top-level positions within oil, gas and energy companies such as Hydro, Equinor, Aker and Engie. She has served as a board member of multiple Scandinavian industry leading companies – including Det norske oljeselskap ASA, Electromagnetic Geoservices ASA, and Yara International – over the past twenty years, with current, active board member positions at Alfa Laval, Scatec Solar and Oslo Bygg. She was previously deputy CEO and COO at Europe’s leading oil and gas company, Wintershall DEA. Wastefront has also announced its first £25 million tyre recycling facility will be built in the UK.
Could Covid impact lead to widespread ‘dead-end’ stockpiling of waste tyres?
The Tyre Recovery Association outlines its concern that high recycling prices combined with cashflow problems for tyre businesses could lead to ‘an ugly and very expensive problem
The Tyre Recovery Association is urging the Environment Agency to be more vigilant about stockpiling waste tyres. The association is concerned that the current relaxation of stockpile permitting rules could lead to operators storing more waste tyres than they can handle. With recycling gate prices high and cashflow under enormous pressure, the temptation to accept unrealistic collection price offers is great. However, if the collector is unable to process waste tyres as a result, abandoned waste tyre stockpiles could become “an ugly and very expensive problem”, which could prove damaging to the reputation of the tyre business as a whole.
Enviro and Michelin extend strategic partnership letter of intent
Enviro and Michelin have extended their recently signed letter of intent regarding a strategic partnership between Scandinavian Enviro Systems (publ) and the French global tyre manufacturer until October. The original exclusivity agreement built into the initial letter of intent was due to run out on 31 July and would have meant that Enviro couldn’t co-operate with other tyre manufacturers and tyre suppliers until after this date. That too has been extended until the end of October.
Initially the two parties expected that a final agreement would have been reached by the middle 2020, but the negotiations have been delayed at least partly due to the ongoing pandemic.
UK could lose out to Europe in battery recycling market
The UK is at risk of losing out to the rest of Europe when it comes to the automotive lithium ion battery recycling market, according to a new research report published this week by WMG at the University of Warwick and backed by the Advanced Propulsion Centre UK, the High Value Manufacturing Catapult and Faraday Battery Challenge at Innovate UK.
The new report entitled “Automotive Lithium ion Battery Recycling in the UK” by Anwar Sattar, David Greenwood, Martin Dowson and Puja Unadkat in WMG, at the University of Warwick calls for the UK to move quickly to establish commercial scale recycling for automotive lithium ion batteries.
Tyre particulate solution wins James Dyson Award
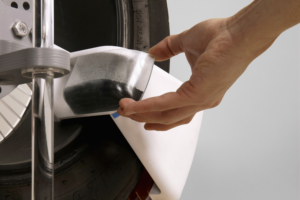
The Tyre Collective aims to reduce particulate via a device fitted to the wheel, which uses electrostatics to collect particles as they are emitted from the tyres (Photo: The Tyre Collective)
The Tyre Collective – winners of the James Dyson Awards 2020 – have designed a device to capture tyre particulate at source. According to the UK Department for Environment, Food & Rural Affairs’ “Air Quality: Brake, Tyre and Road Surface Wear” report, tyre-wear accounts for nearly half of road transport particulate emissions. Furthermore, a reported half a million tonnes of tyre particles are produced annually in Europe alone, from vehicles accelerating, braking and cornering. As we move towards electric vehicles in the future, exhaust emissions will reduce but tyre particles will continue. The Tyre Collective estimate that tyre emissions may even increase, as electric vehicles become heavier due to the added battery weight. For both reasons, this year’s UK national James Dyson Award winners attempt to address this issue (click here for an overview of the latest tyre wear particular research).
Australian tyre recycler expanding into Europe
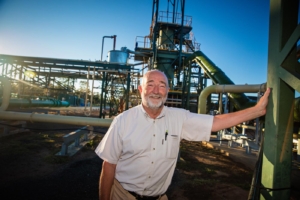
The UK, Greece and Italian projects are on the horizon, but the question of which facilities will appear first hasn’t yet been answered (Photo: Green Distillation Technologies)
As we reported last month, Australian tyre recycler Green Distillation Technologies (GDT) believes the time is right for them to expand internationally. Now the company is highlighting its intentions to move into the European market. Tyres & Accessories understands that Greece and Italy are at the top of the list, but talks are also ongoing in the UK.
Explaining why Europe and why now, GDT chief operating officer Trevor Bayley said that the recent statement by Fazilet Cinaralp at the webinar organized by the Bureau of International Recycling (BIR) who said that only 42 per cent of the 12 million tonnes of end-of-life tyres (ELTs) generated in Europe each year are recycled, had heightened GDT’s interest
Green Distillation Technologies considering UK and other international markets
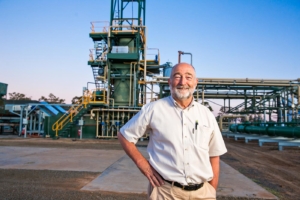
Trevor Bayley, COO Green Distillation Technologies, pictured in front of the firm’s processing facility in Warren, Western New South Wales (Photo: GDT)
Australian tyre recycler Green Distillation Technologies, which recycles tyres according to a kind of pyrolysis process, is considering expanding into the UK and other international markets.
Expansion began with an agreement with a tyre collection business who are so confident in the Australian technology that they have increased their commitment to GDT from 10 tyre recycling facilities across the US to 15 with the construction of three key plants to commence as soon as the regulatory agreements and government approvals are obtained.
SME uses recycled tyres for innovative pothole repair solution
British motorists pay a high price for repairs to damage caused by potholes. Claims for pothole damage are estimated to total around £4 billion annually, according to insurer Green Flag. And such is the public outcry over the state of the country’s roads that the government set aside a fund of £2.5 billion in the latest Budget to address the problem. To addres this, Roadmender Asphalt, a Sheffield-based bitumen technology company, has developed a novel approach to pothole repairs. The company uses mastic asphalt, one of which is called Elastomac. This novel thermoplastic includes seven end of life tyres in every tonne.
Tyre reuse & processing rate rising in Australia
According to a report published by Tyre Stewardship Australia (TSA), 69 per cent of the 466,000 tonnes of end of life tyres generated within the country in 2018-19 were recovered for reuse or processing into tyre derived products or in thermal processing. This amount is the equivalent of 40.3 million car tyres.
The 40.3 million tyres equivalent can be accounted for as follows:
Reuse: 85,000 tonnes, the equivalent of 10.6 million used car tyres
Tyre derived products: 190,000 tonnes, the equivalent of 23.8 million car tyres
Thermal processing: 48,000 tonnes, the equivalent of 5.9 million car tyres