2024 marks 50 years of Bulldog and 20 years of Bridgestone partnership
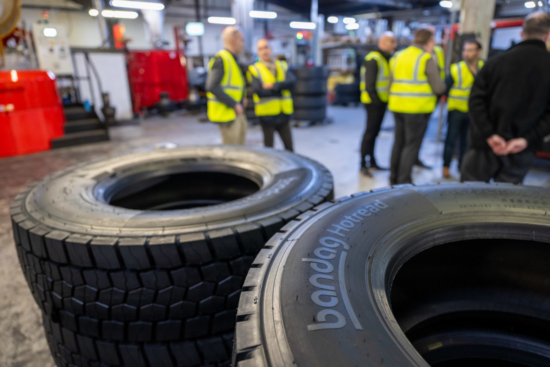
The Bulldog operation was founded in 1974 as part of the Sleaford Tyre Company Group and first supplied retreads to Bridgestone in the mid-1990s, before Bridgestone purchased it outright in 2005. A significant part of Bulldog’s recent history is made up of an increasingly close collaboration with Bridgestone. To be more specific, the two companies started working together in 1992, when Bulldog began making test tyres for Bridgestone. By 1995, Bulldog had become a major Bridgestone retreading partner. 10 years later, the working relationship became closer still when Bridgestone bought Bulldog. And next year market the 20th anniversary of Bridgestone’s Bulldog ownership. In the intervening years, Bridgestone global bought leading pre-cure retreading franchise, Bandag. Meanwhile, in the UK, Bridgestone grew to a position of market leadership in the bus tyre segment around 2017.
All this context is important because it explains the background to the establishment of what was internally known as “project mercury” in 2020. Project Mercury is the working title for the numerous upgrades that have now been completed at Bulldog, but also alludes to the increased emphasis on hot retreading that is now evident at the Bourne, Lincolnshire factory.
In 2022/23 Bridgestone introduced the Bandag Hotread concept, that – it must be said – is something of a divergence from the well-known roots of the pre-cure centric Bandag name. Project Mercury’s impact on the Bulldog factory meant moving out pre-cure-orientated autoclaves in order to make room for more mould-cure curing presses. Indeed, Bridgestone has brought in eight new curing pressures that are said to bring with them a 15 per cent reduction in energy consumption.
At the same time, Bridgestone has installed two new automated buffers at Bulldog, which offer 25 per cent energy reduction, 10 per cent cycle time improvement and are digitally integrated into the factory.
The installation of TRM-manufactured Black Dragon/Black Swan automated extruder/tyre builder technology is said to bring with it a 20 per cent improvement in cycle time, a 10 per cent energy reduction, while reducing employee handling.
The Basys system has also been installed on-site. This fully digital solution offers paperless tracking from casing collection to retread delivery. All of this was installed between September and December 2023 as part of the two-to-three-year Mercury project.
Understanding Hotread
So why the emphasis on so-called hot retreads? With the launch of Hotread, Bandag will now offer both pre-cured and mould-cured retreads. “Due to customer demand, we are now ramping up production of hot-cure retreads, which will grow our market share accordingly. These mould-cured retread tyres feature the same performance as the Bandag premium pre-cured tread range”, company representatives explained, adding:
The installation of a Black Dragon/Black Swan tyre builder is at the centre of raft of investments made in the Bridgestone Bulldog retread factory (Photo: Bridgestone)
“With the extension of our hot retreading portfolio, we are responding to market demand and offering our fleet customers an extended range of premium retreading solutions. We will continue to offer precure (cold) retreads in addition to Hotread, allowing fleets to select the right tyre for their application and wheel position.” Visual aesthetics is said to have been a key driver and, more specifically, the new Bandag sidewall design, which is designed to offer a ”look-like-new appearance,” which Bridgestone reports, is “more and more customers want”.
Since Bandag was historically a pre-cure retread brand and Bulldog has manufactured both kinds of retreads, the latest investments raise the question: what is currently the split between hot and cold?
“For many years the Bulldog plant has used both production processes, but with cold contributing around 60 per cent of the total volume. With the new focus on market-leading hot cure products we expect the production to more closely mirror the UK market which is estimated at around 75 per cent hot retreads”, came the official answer.
To put this into context, according to Bridgestone, the European market is split roughly 50:50 between hot and cold, while in North America (the world’s largest retread market) cold makes up the vast majority. With that in mind, it is clear that the UK market approach is something a bit different. So will the Bulldog approach be replicated in other European markets?
“The pre-cure:hot-cure set-up and context can be different in each market…Not every market is arranged as in the UK.” Andrea Manenti explained to Tyres & Accessories, adding: “Germany and France have Bulldog-like aspects. Other markets are more reliant on franchisees. Market demand is key.” But ultimately, “some markets that were previously pre-cure dependent may now get hot options”. These ideas are very much at an early stage of planning, but while each market has their own conditions, it is clear that the Bulldog/Hotread roll-out is not designed to be a unique or isolated case and the Bulldog example could potentially even be seen as something of an initiator of similar transitions in other European market. The Bridgestone approach is “glocal” in that respect, which reflects wider Bridgestone environmental and sustainability philosophies, according to Manenti.
And retreading is an inextricable part of that sustainability philosophy. As well as being a inherently sustainability focused by virtue of being a retreader, in 2022, Bulldog recycled 520 tonnes of rubber dust and 4500 scrap tyres. With Bridgestone aiming for 50 per cent reduction in carbon emissions by 2030 and to be carbon neutral by 2050 – that emphasis is only going to increase.
Comments