Marangoni invests 8 million euros in Rovereto production
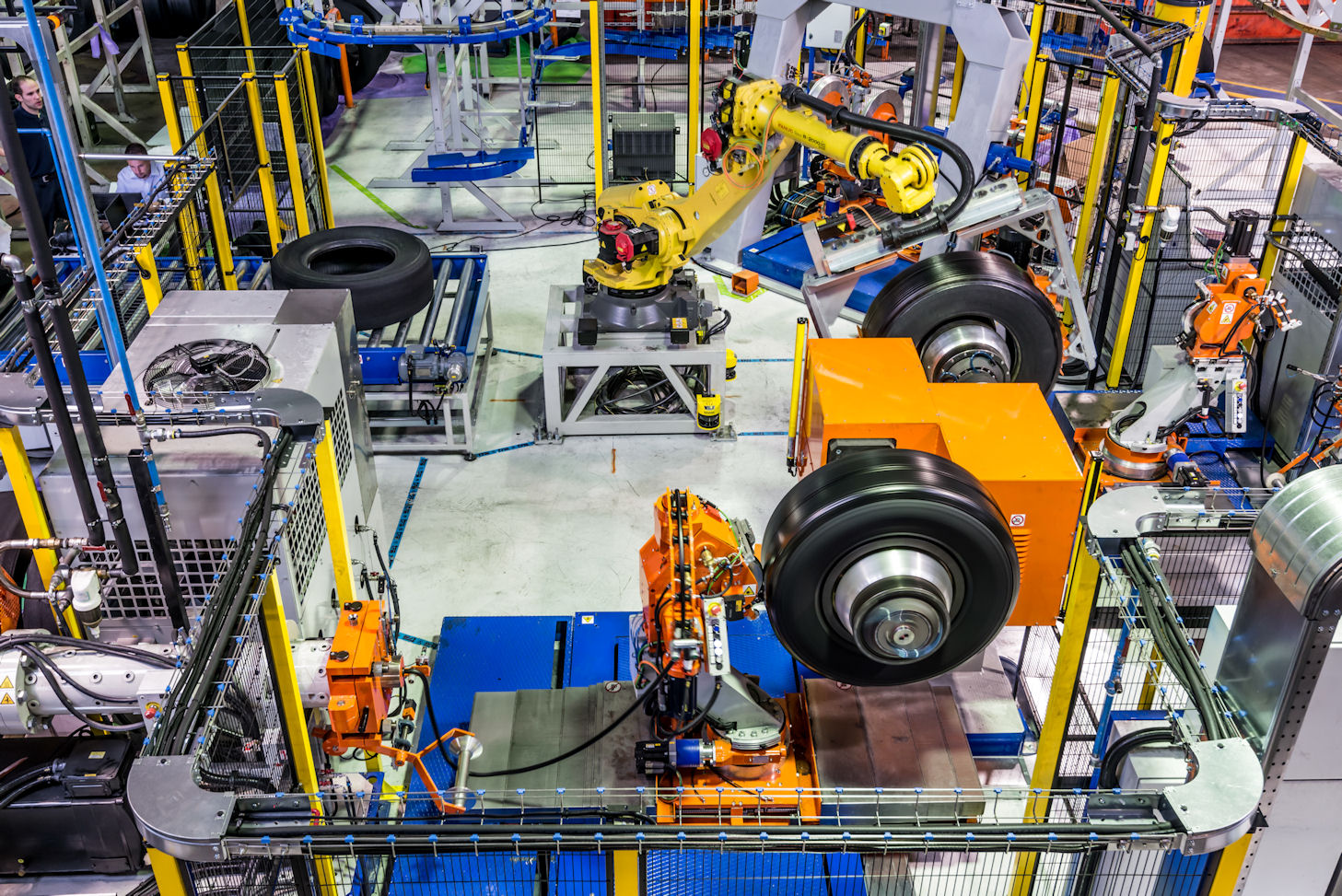
As the deadline approaches for a possible extension of the labelling requirements already in force for new tyres to also include retreads, the retreaded truck tyre segment is rapidly evolving both in regards to performance and the level of uniformity and efficiency that must be guaranteed in order to comply with an evolving legislative situation. With its constant commitment to innovation and development of new product and process technologies for truck and earthmoving tyre retreading, the Marangoni Group has recently introduced and started implementing a multi-year investment plan worth around 8 million euros aimed at modernising the various production departments at its Rovereto plant.
The main news involves the purchase of a new, latest-generation mixer, capable of meeting demand for increasingly sophisticated and high performance compounds. This new Banbury, currently being installed and expected to be ready by the end of 2015, features rotors with variable intermeshing clearance and can produce compounds with extensive filler dispersion, a fundamental requirement for achieving treads with very high mileage and, at the same time, low rolling resistance. The new Banbury mixer will also improve the quality of earthmoving tread compounds, making them more competitive for heavy-duty applications.
Another important investment made in recent months concerns the building of mould cure retreads in a production ‘island’ (see photo), in other words, a system that manages the entire tyre retreading process, fully automatically and flexibly. Constructed exclusively for the Rovereto plant, this production line features four extruders served by an industrial robot that applies the cushion gum and the tread using spindles, controlling the amount of rubber placed on each tyre by measuring the weight and the movements performed by the robot. The entire process is managed and monitored using special prototype software that can generate profiles interactively.
“The new technology applied brings significant improvements in the final products, both in terms of quality and performance, making them increasingly comparable to premium new tyres. The highly automated process also ensures greater flexibility and efficiency, reducing processing times and allowing more flexible management of production flows,” reported Marangoni in a press statement.
Other upgrades are being made to the vulcanisation department, with the purchase of presses that can house 12 sector cylindrical moulds and that will further improve product uniformity by reducing the relatively frequent phenomena of ovalisation and unbalance when retreading a used tyre.
Massimo De Alessandri, Marangoni Spa CEO, stated: “I’m more and more convinced that there will be many opportunities for quality retreads in the future, and this is the focus of the efforts we are making to improve processes and increase efficiency at the Rovereto plant. The significant investments we have made, exploiting the day-to-day experiences at the factory and the innovations of our Group companies operating in the mechanical sector, mean we can continue to perfect our technological development process and strengthen our cooperation with other players in the sector, for whom our company has always represented the reference partner in developing their projects in the retreading sector.”
Comments