Speak out against wheel theft: Ford develops ‘vocal’ 3D locking nuts
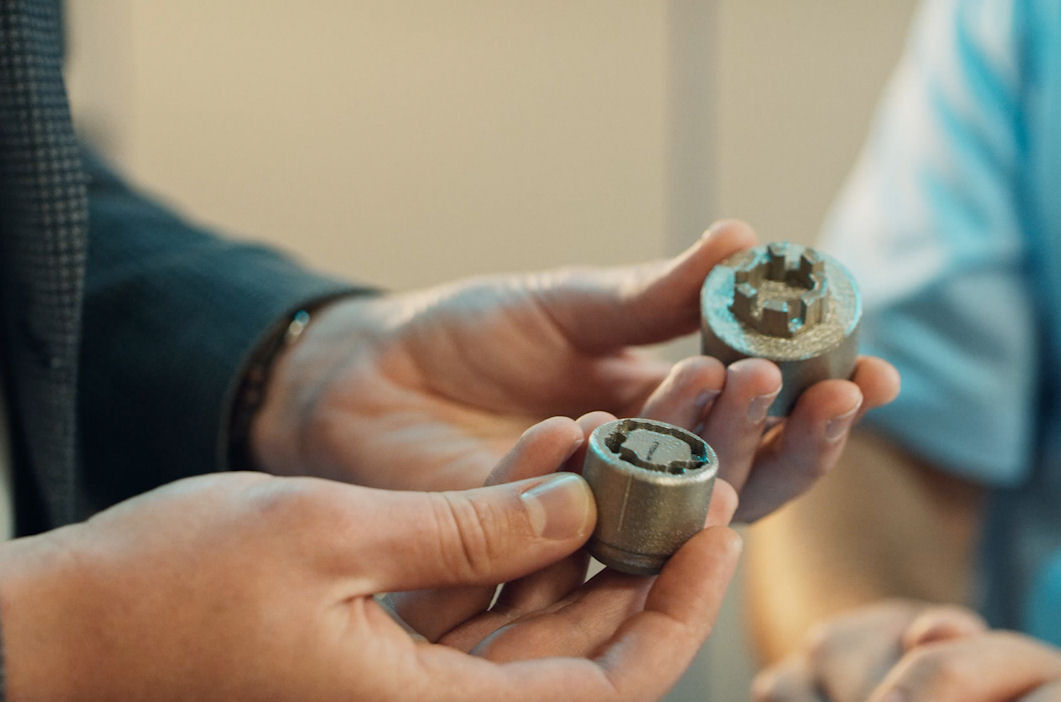
As car security systems become increasingly sophisticated, thieves are turning their attention to car parts instead. This is bad news for owners of vehicles fitted with alloy wheels, but Ford now offers a way of keeping those wheels yours – and the solution is guaranteed to get car owners talking.
Ford is taking the locking wheel nut a step further. Instead of relying upon an adaptor or key to loosen the nut, the vehicle manufacturer’s engineers have teamed up with industrial 3D printing specialist EOS to develop locking nuts that feature contours based upon the driver’s voice.
Like an iris scan or a fingerprint, a person’s voice can be used as a unique biometric identification. Engineers record the driver’s voice for a minimum of one second, and use software to convert that singular soundwave into a physical, printable pattern. This pattern is then turned into a circle and used as the design for the locking nut’s indentation and key.
With the geometry in place, the nut and key are designed as one piece, then 3D-printed using acid and corrosion-resistant stainless steel. When finished, the nut and key are separated. Only a small amount of grinding is then required to make them ready for use.
The design also includes second-level security features that prevent the nut from being cloned or copied. The unevenly spaced ribs inside the nut and indentations widen the deeper they go. This prevents thieves from making a wax imprint of the pattern, as the wax breaks when pulled from the nut.
According to Ford, the 3D printing process can be paired with wheel nuts in other ways. Instead of employing the driver’s voice to create the contours, the nuts could feature designs specific to a vehicle, such as the Mustang logo, or use the driver’s initials. A design could also take inspiration from a driver’s interest and use, for example, the outline of a famous race circuit.
Expanding the use of 3D printing
3D printing, or additive manufacturing, offers design flexibility to help reduce weight, improve performance and create parts that wouldn’t be possible using conventional methods. For more than 30 years, Ford has increasingly used 3D printing to make prototype parts which help reduce the development time for new vehicles.
The company has also used this technology to create parts that feature in the Ford GT, Focus and Mustang GT500, and will make more 3D-printed parts in the future. Bespoke car parts are also 3D printed, including the intake manifold in Ken Block’s Hoonitruck and the pair of wind louvres found on the M-Sport Ford Fiesta World Rally Championship car.
On the Ford production line, 3D printing is used to create assembly line tools that are up to 50 per cent lighter, which makes repetitive tasks less physically stressful and helps improve manufacturing quality. As many of these tools are made of nylon, Ford has introduced a recycling programme that turns old 3D-printed pieces and plastics from manufacturing areas into 100 per cent recycled nylon. Ford also creates 3D-printed safety equipment, such as protection sleeves for rotating tools used on the production line, which prevent operators from incurring finger and arm injuries.
“It’s one of the worst experiences for a driver, to find their car up on blocks with all four wheels gone,” comments Raphael Koch, Ford Advanced Materials and Processes research engineer. “Some alloy wheels can cost thousands to replace, but these unique rim nuts will stop thieves in their tracks. Making wheels more secure and offering more product personalisation are further proof that 3D printing is a game-changer for car production.”
Comments