Retreader Reifen Apel achieves continuity through focus on quality
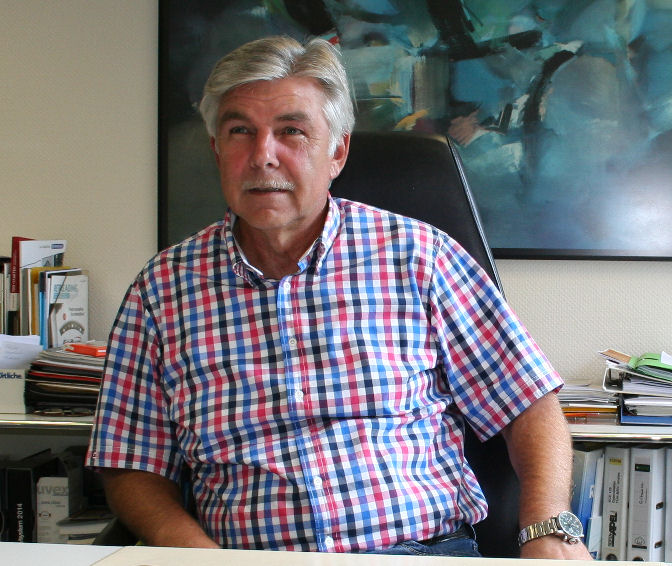
There’s a lot of talk within the tyre market at the moment – particularly in the retreading business – about tyres imported from the Far East, tyres that sometimes cost barely half as much as a new, European-made truck tyre and therefore make life very hard for many retreaders. But even though the market weakness that follows these imports is a point of concern for all involved, the problems that arrive along with these budget tyres don’t affect everyone equally. German retreader Reifen Apel, for example, has long understood the value of building up a market and clientele that follows its credo of absolute product quality – customers such as these rarely succumb to the temptation of lower purchase prices. Speaking with Tyres & Accessories, company manager Udo Lossau explained how and why investment in production, and through this in products, always pays off.
“Everyone creates a market for himself over the years,” says Lossau. The Reifen Apel story begins in 1947 with the establishment of a vulcanising operation in the town of Korbach by Paul Apel – who until that time was in charge of inner tube production at the nearby Continental tyre plant – and his son Frank, who like his father was also a trained and experienced tyre mechanic craftsman. The two men gradually expanded the operation, and Lossau recalls that they’d already built it up into an impressive retreading business by the time he married Frank Apel’s daughter Sibylle in the 1980s.
The son-in-law’s entry into the business (today he heads the limited liability company together with wife Sibylle) was followed by a period in which some major decisions crucial to the company’s future needed to be made. Lossau himself contributed to this in no small way when a couple of particularly important decisions were reached in the late 1980s: Should Reifen Apel continue to retread passenger car tyres, and should it remain faithful to mould cure truck tyre retreading? The company was already well-established as a pre-cure retreader – it adopted the pre-cure procedure as far back as 1974, making it one of the first retreaders in Germany to use it – and over the years had built up a degree of expertise. Pre-cure treads and the pre-cure process had a much better reputation in those days than the materials available for mould cure retreading, and therefore the quality of Reifen Apel’s pre-cure retreads were far superior to that of a typical mould cure retreaded tyre. Upon reaching decision crunch time regarding investing in mould cure retreading – the company operated five passenger car tyre presses and four truck tyre retreading presses at the time – Lossau decided against proceeding further in this direction. Demand for retreaded passenger car tyres was following a downward trend and production volumes were also insufficient for viable mould cure truck tyre retreading.
Reifen Apel completely devoted itself to pre-cure truck tyre retreading in 1989, and since then the operation has grown consistently. Today it forms an economic mainstay of the business, together with three company-owned outlets that sell the lion’s share of the 15,000 tyres the retreader and full-range retailer produces each year.
Udo Lossau attributes the stable demand for Reifen Apel’s products – it has remained largely unaffected by the flood of cheap Chinese tyres – to the market segment the retreader sells into. “We produce quality and we also want to sell this quality,” he says. But what does Reifen Apel understand as quality? Udo Lossau’s credo is that quality means to check everything twice. The manager is well aware that anyone producing 15,000 tyres per annum is bound to have some rejects. But even though he accepts this as fact, Lossau strives to keep the rate of failures as low as technically possible. For this reason he regularly trains tyre and vulcanisation mechanics at the Reifen Apel facility. These trainees typically become part of the company’s workforce upon fulfilling the requirements of their apprenticeships. Following the three-year apprenticeship they undergo an additional two years of further training that focuses upon various areas closely linked to the more technical aspects of production, including buffing, tread application, vulcanisation and, of course, quality control.
This last area is one the retreader strives to make as watertight as possible. A third of all casings entering the Reifen Apel retreading plant are sourced from the company’s three retail outlets and the remainder come from reputable casing dealers, and even though each and every one is visually inspected by a trained employee during their entry control examination, this is always backed up by shearography. Further technology-driven control, such as pressure tests or the use of nail hole detectors, is not utilised. Instead, an extra control is performed after retreading by subjecting every tyre to shearographic control a second time. This measure is undertaken as previously unseen separation within the tyre sometimes only becomes apparent after it has been heated to 110 degrees Celsius. “We apply shearography like crazy,” says Lossau with a grin. He’d rather separate out close to one per cent of tyres following the retreading process, stamp these with an A8 speed rating (to 40 km/h) and sell them virtually at cost price to agricultural users than risk tyre failure on a truck travelling at motorway speeds. A large majority of Reifen Apel retreads are utilised in long-haul transport.
High production quality can only be guaranteed when manufacturing takes place in facilities containing state-of-the-art technology – this goes without saying, says the managing director. New production control software, largely programmed by Udo Lossau himself (prior to joining the Apel family business he worked in the IT sector) came on stream in late July. The production equipment itself is also constantly serviced and replaced whenever needed. According to Lossau, a production unit seldom remains in operation for more than eight years, or, perhaps occasionally, ten years. Cycles such as this not only increase product quality as equipment developments keep pace with that of new tyres, they also reduce downtime periods that keep the company’s seven production employees away from tyre manufacture. One significant exception to this eight to ten year rule exists, however: The autoclave. The autoclave at Reifen Apel can accommodate 20 tyres and is heated by self-produced steam, and this unit has been in use for decades.
Reifen Apel also places great value on the quality of the materials it uses. The retreader cooperates closely with German retail network Vergölst and with Continental – no great surprise there, as Continental employs around 3,000 people in Reifen Apel’s hometown of Korbach and its products dominate the regional tyre market. Reifen Apel is also a ContiTread pre-cure retreading partner, but treads from Kraiburg Austria have nevertheless dominated the retreader’s range for many years. “We’re bonded to Kraiburg,” comments Udo Lossau. He is a great advocate of Kraiburg’s product classification and considers the K_plus premium treads to fully meet his own expectations for quality. Retreads optimised for mileage and rolling resistance reduce total cost per mile, and in sales talks the managing director aims to persuade customers that superficial marketing based on a tyre’s purchase price makes no real sense.
Recent weakness in the commercial vehicle tyre market has affected Reifen Apel as much as others. While Germany’s new tyre market developed in a comparatively stable manner and ‘only’ decreased by three per cent in the first half of 2015 (according to WdK sell-out figures), retread market volume contracted by around 13 per cent during the same period, and pre-cure retreading was overrepresented with a decrease of 18 per cent. Much pressure has come from imports of low-cost new tyres from the Far East, but this is something that Lossau cannot confirm from his own market experiences; from within its clientele Reifen Apel has – if at all – only appeared to have lost a small amount of business. “We have reliable partners, and this is important,” comments Lossau. The new and retreaded commercial vehicle tyre business accounts for around 50 per cent of Reifen Apel’s turnover.
One part of this commercial vehicle tyre business is very new and lies close to Udo Lossau’s heart: Reifen Apel recently began cooperating with Continental in the retreading of the industrial tyres the German giant first presented at the CeMat show last summer (Conti LifeCycle). Reifen Apel specialises in the entry control and buffing of these tyres, and Continental then applies treads and vulcanises the tyres in its own new tyre factory next door. The buffing of these Continental industrial tyres doesn’t take place according to standard procedure using conventional buffing machines, instead it is a fully automated process. The tyre is placed on its side and two robots, developed and patented by Udo Lossau, perform the operation. Visitors to the Reifen Apel facility may marvel at the technology, however photography is not allowed. This facility has been running at full strength since it entered operation last year, says the managing director in closing.
Comments