Bosch: Digitalisation to be decisive within the automotive aftermarket
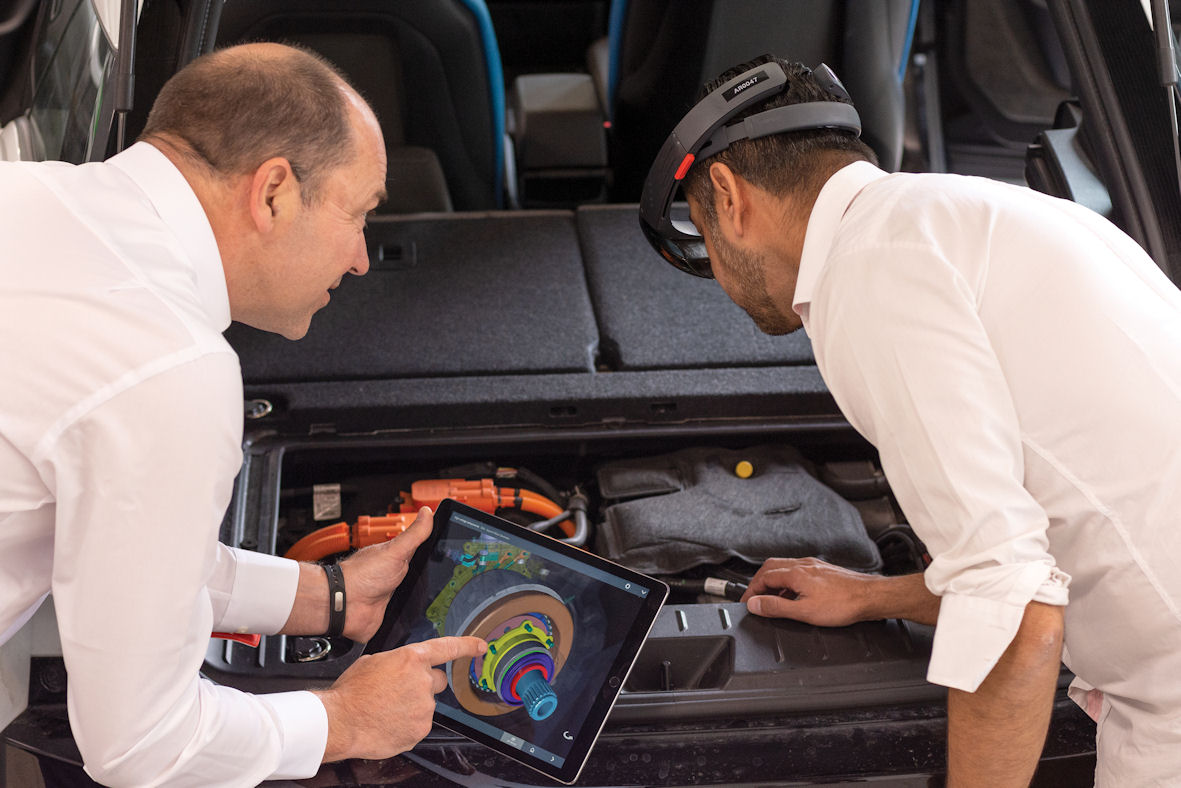
According to auditing and consulting company PwC, more than 470 million connected vehicles will be plying the world’s roads and motorways by 2025. This significant growth will be accompanied by rising demand for aftermarket software and data services, and vehicle connectivity will become a decisive factor for the sector’s future expansion. CLEPA, the European Association of Automotive Suppliers, anticipates that the market for software and data services in Europe alone will treble to approximately 34 billion euros –about 140 euros per vehicle – by the middle of the next decade.
Against this backdrop of expected growth, vehicle connectivity was a key focus for Bosch Automotive Aftermarket at Automechanika Frankfurt last week. Manfred Baden, president of the Bosch Automotive Aftermarket division, stated at the fair that connectivity, automation and new drive solutions will have a “significant impact” upon the automotive industry as vehicles become increasingly sophisticated. He added that Bosch is already increasingly relying upon connected and database solutions to make processes within workshops speedier and more efficient.
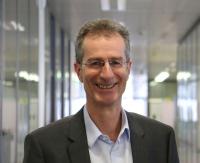
Manfred Baden expects connectivity, automation and new drive solutions to have a “significant impact” upon the automotive industry
Bosch Automotive Aftermarket, with its 17,000 employees, is part of the Bosch Group’s Mobility Solutions business, an operation whose turnover increased 7.8 per cent year-on-year in 2017 to 47.6 billion euros last years. Baden stresses that this above market level of growth will continue in 2018. “Our industry is on the brink of an evolution which will be both a challenge and an opportunity. Opportunities exist for all companies focusing on digitalisation and connectivity in a timely manner. Bosch Automotive Aftermarket is also focusing more than ever on the range of connected products and services.
“With innovative concepts for effective and efficient maintenance and repair throughout the complete product life cycle as well as connected solutions for diagnoses and workshop processes, we support our partners concerning both current and future vehicle stocks,” he added.
Connectivity and new database solutions hold the potential to optimise workflow within workshops and garages while offering significant time savings. Bosch Connected Repair workshop software, for instance, prevents the time-consuming duplication of work – when a vehicle requiring repair is registered on the system, data on this vehicle can be accessed on all PC-based systems. And in future, Augmented Reality will aid workshop employees perform even sophisticated repair tasks. Bosch believes the application of technology will result in average time savings of up to 15 per cent. The company received an Automechanika Innovation Award this year in the Alternative Drive Systems & Digital Solutions category for its efforts in this field, specifically its Bosch Common Augmented Reality Platform (CAP).
Preventing duplication of work through connectivity
Bosch Connected Repair provides a basis for the intelligent connectivity of diagnostic hardware used in workshops. It connects vehicle reception, vehicle information and test devices and creates a common database that can be wirelessly transmitted to all connected devices. This means that a vehicle must only be identified once instead of being individually registered on each device as was the case in the past. The benefit of this can be measured in time saved; Bosch estimates that compared with service and maintenance using Bosch products without Connected Repair, the use of the connected technology results in time savings of up to ten minutes per vehicle at the workshop. Test reports, comments and images are directly stored in the digital job card and can be retrieved at any time. All employees can easily access the digital job card and vehicle status at any time.
Finding the best repair solution via collective intelligence
In addition to developing diagnostic hardware with intelligent connectivity, Bosch Automotive Aftermarket is also working on the further development of established software. The new version of its Esitronic 2.0, for example, allows workshops to optimise repair and diagnostic procedures to decrease the time required for each vehicle and to perform continuous online updates. Furthermore, it can be used both online and offline. With the help of a free text search and a document preview, users can find necessary information easily and quickly.
The experienced-based repair function provides yet another advantage. This utilises a Bosch database containing more than 750,000 actual use cases. Once a known error is recognised during a diagnosis it automatically recommends a repair solution compiled by Bosch experts that other users have already assessed as a good solution. All current subscribers will receive Esitronic 2.0 as a free online update.
KTS 250 diagnostic tester
Esitronic is the centrepiece of the new compact KTS 250 diagnostic tester that Bosch debuted at Automechanika. Suitable for smaller workshops or as an additional mobile device in larger workshops, KTS 250 offers comprehensive vehicle coverage of about 150 passenger car brands. Futureproofing comes courtesy of the unit’s integrated DoIP Ethernet interface and automatic vehicle identification supported by a VIN database.
Short set-up times for the calibration of cameras and sensors
Driver assistance systems are being fitted to an increasing number of vehicles. Bosch has developed suitable hardware and software solutions in case a video sensor needs to be calibrated after replacing the windshield. Using the Bosch ADAS – for Advanced Driver Assistance Systems – calibration system, calibrations on radar and video sensors can be performed both quickly and accurately, with the Esitronic software controlling the vehicle-specific calibration and adjustment procedures.
Augmented Reality
Bosch says it is breaking new ground with the application of its Augmented Reality (AR) solutions for the training of workshop and garage technicians, and as mentioned, its work in this area was recognised at this year’s Automechanika Innovation Awards. Bosch first sketched its vision of a connected workshop utilising AR back in 2014.
The specific benefits of AR technology have been determined through a field study carried out at Bosch Car Service workshops: By using AR applications, average time savings of 15 per cent for each step taken are possible even on commonplace vehicles and less sophisticated repair tasks. This allows the mechatronics, for instance, to locate hidden components rapidly and receive work instructions or information on required special tools integrated into the real image.
Bosch has developed several new training methods for training workshop staff based upon Augmented Reality, including current training in the field of electromobility. With the assistance of AR, technicians undergoing the electromobility training are taught the differences between hybrid and fully electric vehicles, the functions and characteristics of various high-voltage components as well as strategies for troubleshooting.
Comprehensive parts supply
Alongside new developments, Bosch Automotive Aftermarket states that conventional spare parts also continue to be important part of its business. From new parts to series-remanufactured replacement parts and repair solutions, Bosch supplies matching spare parts for almost any type of vehicle – solutions that draw upon decades of experience in the original equipment sector.
Comments